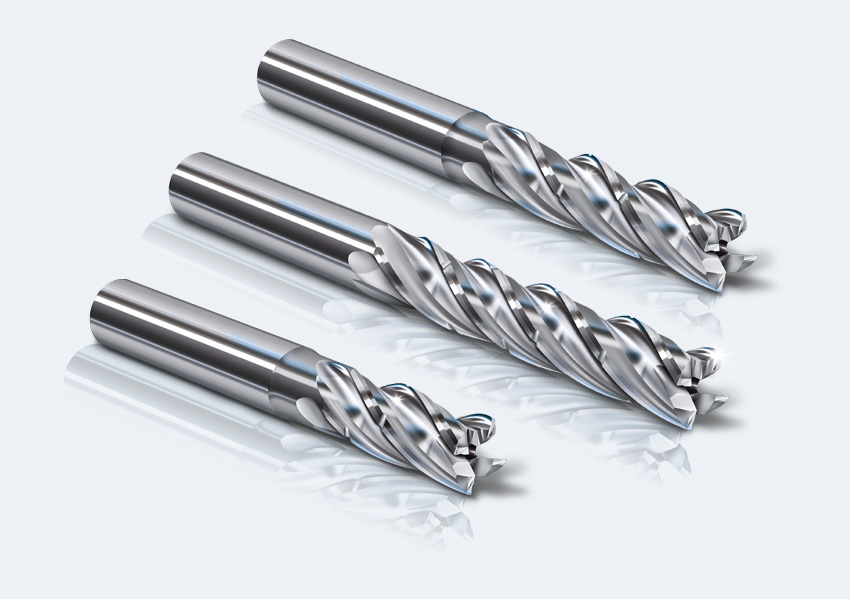
Multifunctional High-performance Milling of aluminum and non-ferrous metals
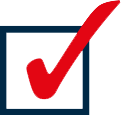
Maximum chip removal rate, reduced production costs
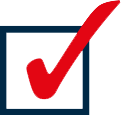
Outstanding surface and component qualities
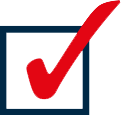
Shorter machine setup times for fast application
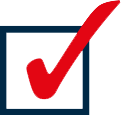
HDC capable and process reliable
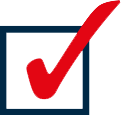
Sustainable thanks to FRAISA ReTool® Services
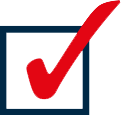
Perfect application data
Material:
Simple milling of aluminum, plastics and copper
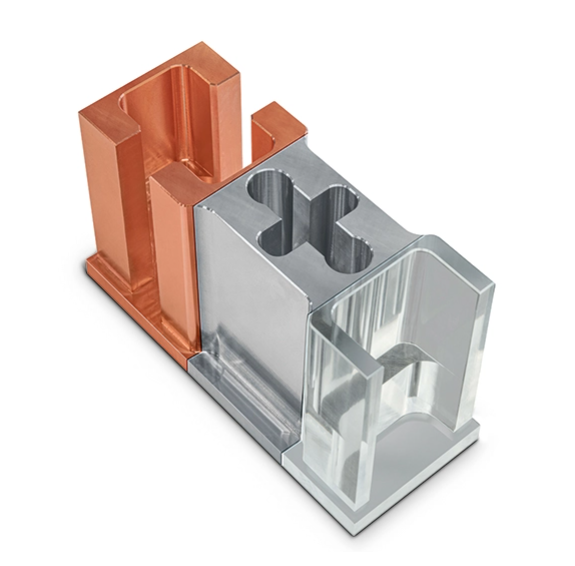
The successful milling of aluminum, plastics and copper is a major challenge. With the completely newly developed MFC Alu milling system,
FRAISA provides you with the solution for reliable machining of aluminum, copper, plastics and other non-ferrous metals.
Wrought aluminum alloys are soft and sticky - there is a high risk of the chips sticking. It is therefore important to quickly remove the chips
from the cutting zone using suitable milling cutters for aluminum with an extremely smooth surface. Our engineers have equipped the MFC aluminum milling
cutters with highly polished, finely balanced flutes and chip breakers. This ensures that chips are removed quickly and chip problems are a thing of the past.
Plastics (thermoplastics/polymethyl methacrylate) are also not easy to mill. They are very soft and warp easily. For elastic and thick plastics,
sharp milling cutters are recommended, which should be used at lower speeds. Our MFC aluminum milling cutters are designed to mill plastics as fine as
silk and without steps or burrs. You can find tips on calculating the right cutting speed in our FRAISA ToolExpert® cutting data calculator.
Copper is very sticky and soft. It has a high elongation at break and is more abrasive than normal aluminum. Milling cutters for copper should
therefore be very wear-resistant - like the new MFC aluminum milling cutters, which make trochoidal milling much easier.
Machine:
The right milling cutter for your machine environment
The multifunctional tools are ideal for carrying out various applications at a high performance level - regardless of machine concepts,
spindle speed or dynamic ranges. This makes the new milling system the best choice for all industries and components. It can be used for
a machining depth of up to 5.2xd as well as for the extremely efficient HDC machining (High Dynamic Cutting / trochoidal milling).
Easy to use: Using MFC aluminium milling cutters simplifies your production process and makes it more efficient, as downtime due to tool changes is minimized.
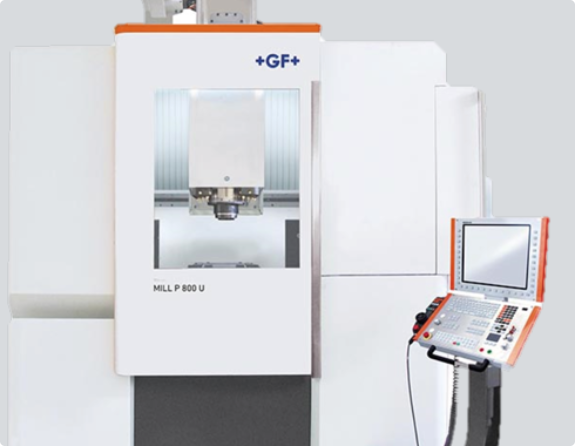
Application and cutting data:
Calculate rotational speeds, cutting speeds and feed rates
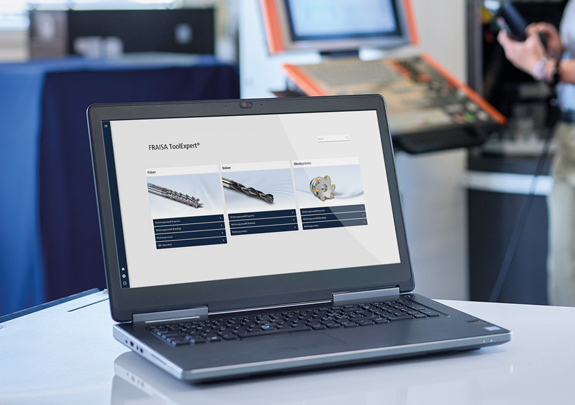
Milling aluminum means high speeds: The FRAISA ToolExpert® provides you with the appropriate application recommendations and cutting data
for the MFC aluminum milling cutters. Our cutting data calculator can be used to determine the appropriate application data and calculate
rotational speeds, cutting speeds and feed rates.
The right data is available for every possible application for all milling cutters in the MFC Alu range - for individual applications as well as
for combinations of different applications or tools.
The data was determined by our FRAISA application experts in many test trials. They are so reliable and efficient that they can also be used
for autonomous processes. If you have individual questions about the optimum application of MFC aluminum milling cutters, FRAISA's technical
application consultants are always available to assist you.
For example, the cutting data can be adapted for spindles for lower speeds.
We will be happy to help you so that you can make optimum use of the tools.
Rule of thumb High Dynamic Cutting / trochoidal milling (HDC):
If the axial infeed depth (ap) is reduced ≥ 1.25xd, the feed per tooth and revolution (fz) can be increased by up to 80 % of the metal removal rate (Q) according to FRAISA ToolExpert®.
Rule of thumb High Performance Cutting (HPC):
If the axial infeed depth (ap) ≥ 0.75xd is reduced, the feed per tooth and revolution (fz) can be increased by up to 70 % of the metal removal rate (Q) according to FRAISA ToolExpert®.
Rule of thumb speed adjustment:
If the speed (n) is reduced ≥ 70 %, the feed per tooth and revolution (fz) can be increased up to 100 % of the metal removal rate (Q) according to FRAISA ToolExpert®.
FRAISA - Your technology partner for machining processes
Customer and needs-oriented advice has always been the focus at FRAISA. That is why our technical application consultants will support you personally with all questions relating to our tools and process optimization. We provide you with the necessary knowledge and the appropriate application data for your production. We can also advise you on difficult machining tasks and show you solutions - please contact us for an individual consultation.
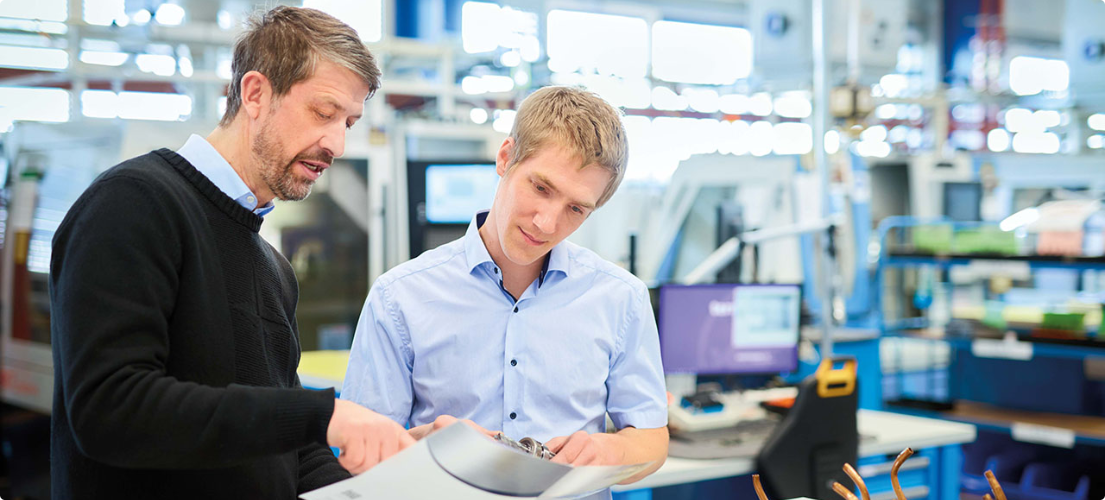
MFC Alu:
Versatile application options and strategies at a glance, which can also be combined:
High Dynamic Cutting (HDC)/ trochoidal milling - Roughing |
High Performance Cutting (HPC) – Penetration |
High Performance Cutting (HPC) - Roughing |
2.5D Pre-finishing |
2.5D Finishing and Superfinishing |
High Dynamic Cutting-Performance (HDC-P)/ trochoidal milling - Roughing |
High Dynamic Cutting-Performance (HDC-P)/ trochoidal milling – Web milling |
High Performance Cutting (HPC) – Slot milling |
High Dynamic Cutting Speed (HDC-S) / trochoidal milling – Roughing and blank cut |
Finishing in one go: Prefinish (PF), Finish (F) and Superfinish (SF) |
High Dynamic Cutting-Performance (HDC-P)/ Trochoidalfräsen - Pocket milling |
Tools and assortment:
Milling cutters for aluminum, plastics, copper and other non-ferrous metals
The extensive range of the MFC aluminum tool family includes 18 cylindrical, smooth-edged milling cutters with shank diameters
from 6 mm to 20 mm in normal, medium-length and extra-long versions (5.2xd).
The new milling system therefore covers a wide range of applications - making time-consuming tool changes a thing of the past.
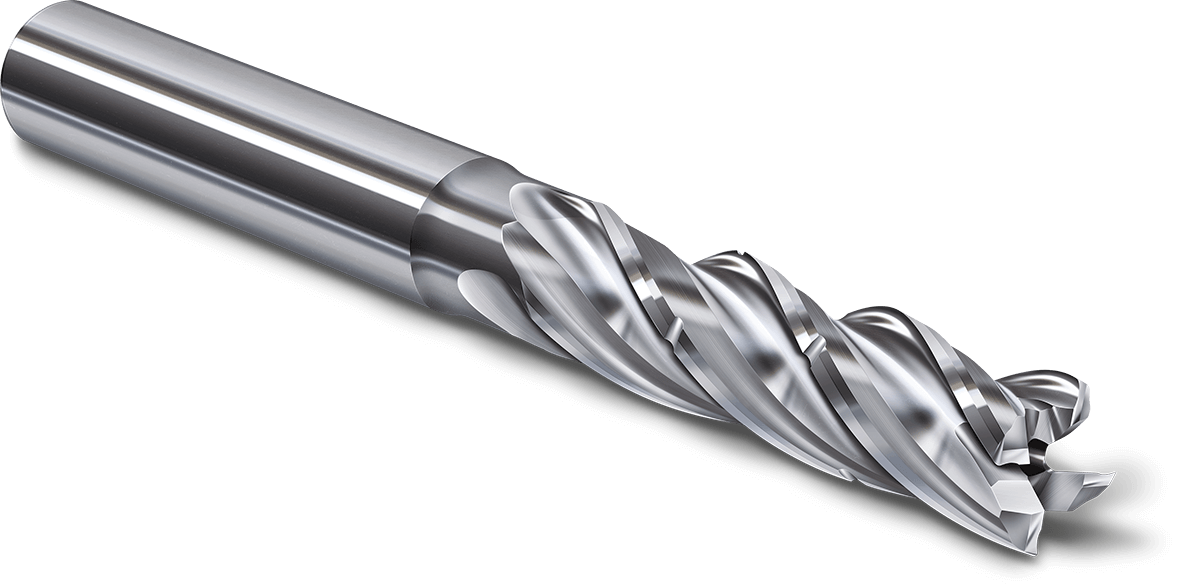
Constant cutting edge length/
diameter ratios
Smooth
transitions
Increasing core
diameter
Precise supporting chamfers
Further developed chip
breaker system
High gloss-ground, finely
balanced flutes
New high-performance
penetration edge
Internal
cooling channel
Corner radius
Outstanding surface and component qualities
Easy to use: Shorter machine setup times and fast application
Flawless chip removal thanks to chip breaker system
Perfect application data in the FRAISA ToolExpert®
Higher productivity, automation and reproducibility
Sustainable service offers with FRAISA ReTool®Services
CAD-CAM programming
The challenge in production is to find the optimum combination of the milling strategy and tool selection. Targets like an increase in productivity
and performance, a longer tool life, process reliability, reduction of costs or an improvement of component quality have to be taken into account
at all times. The faster, simpler and securer a new application case can be solved, the more competitive and effective production becomes.
And right here, the multifunctional high-performance milling (MFC) of FRAISA comes in as the problem solver: The target of the MFC product development
is to simplify the production process without a loss in performance. This allows you to focus on your expertise in CAD-CAM programming and further
increase your competitiveness.
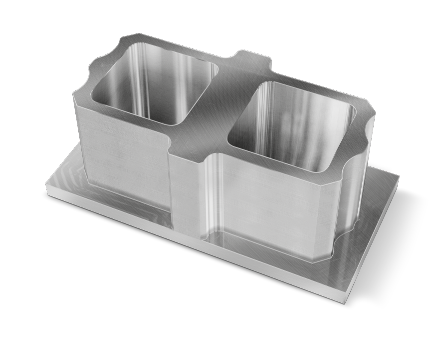
Direct data integration via online interfaces
Through the integration of an XML or JSON interface, a direct import of cutting data from the FRAISA ToolExpert® into the CAM or TDM system is possible. Time requirements and the susceptibility to error are significantly reduced compared to manual data entry. The determined application parameters (cutting and/or geometry data) can be transferred directly to the CAM or TDM system via XML or JSON interfaces. This function is available for hyperMILL® from OPEN MIND, mdm, TopSolid and NX from Siemens. You can find more information on all available interfaces here.
Component:
Perfect surface finishes for your aluminum components
The aim of the MFC Alu range is to simplify your production process for machining aluminum and non-ferrous metals. With our milling cutters for aluminum machining, the right application data and recommendations for use, you can increase your production and performance, achieve longer tool life and improve component quality.
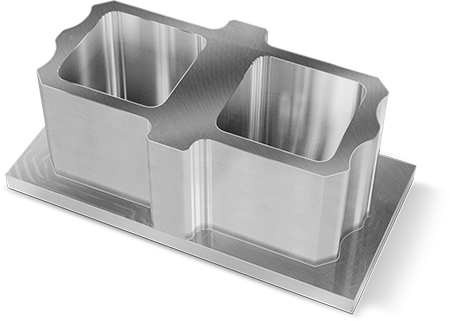
Wrought aluminum alloy component

Total machining time:
approx. 8 min

Material no.:
3.2315

according to DIN:
AlSi1MgMn (EN AW-6082)

Applications:
- High Dynamic Cutting (HDC)/ trochoidal milling - roughing
- High Performance Cutting (HPC) - Penetration
- High Performance Cutting (HPC) - roughing
- High Performance Cutting (HPC) - Penetration
- 2.5D pre-finishing and 2.5D finishing and fine finishing
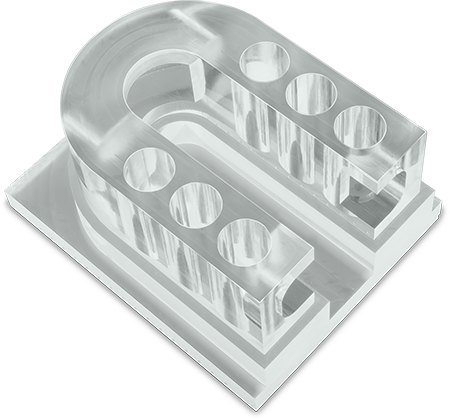
Plexiglas
component

Total processing time:
approx. 8 min

Material no.:
PMMA-GS

according to DIN:
polymethyl methacrylate

Applications:
- High Dynamic Cutting-Performance (HDC-P)/ trochoidal milling - roughing
- High Performance Cutting (HPC) - roughing
- 2.5D pre-finishing and 2.5D finishing and fine finishing
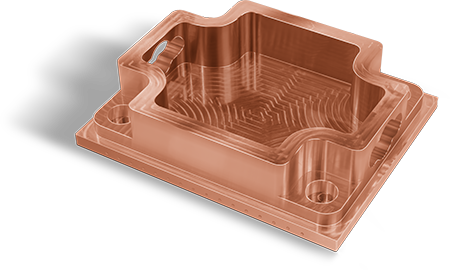
Component
copper Cu-HCP

Total machining time:
approx. 10 min

Material no.:
2.0070

according to DIN
EN 13599/2014

Applications:
- High Dynamic Cutting (HDC)/ trochoidal milling - roughing
- High Performance Cutting (HPC) - Penetration
- High Performance Cutting (HPC) - roughing
- 2.5D pre-finishing and 2.5D finishing and fine finishing
Tool life cycle:
Reduction of CO2 emissions
The environment is an asset worth protecting - which is why FRAISA takes responsibility for the careful use of resources through
extensive measures. We are convinced that industrial production is not at odds with ecological, economic and social sustainability.
The three sustainable services offered by FRAISA ReTool®Services
for industrial tool reconditioning extend the tool life cycle and improve the ecological footprint of your processes. Here you can find
more information about our cost- and resource-saving service offering with performance guarantee.
This component was milled with reconditioned tools that have the same efficiency and performance as new tools.
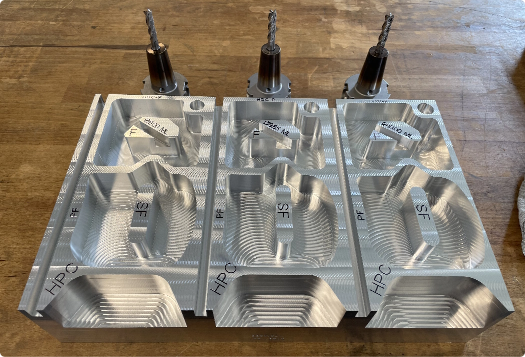