AX: Maximum performance and excellent component quality thanks to innovative technology
The AX range of aluminum milling cutters has undergone continuous development by FRAISA during the last years. In the field of roughing technology, the AX-FPS has set new standards in terms of maximum performance and low power consumption. The cutters are equipped with a speciallly ground roughing profile and an internal cooling channel. Ideal prerequisites for optimum chip removal.
FRAISA ToolExpert® AX-FPS ensures maximum productivity and safety in the respective application thanks to perfect coordination of the tools and machine environment – for cutting depths of up to 5.2xd.
The basis of these new performance horizons: a supporting chamfer technology patented by FRAISA. This involves forming a very highly polished (mirror-finish-ground), very finely coordinated chamfer at the curved and end cutting edges. This dampens any vibrations that occur and improves the milling properties in an impressive manner.
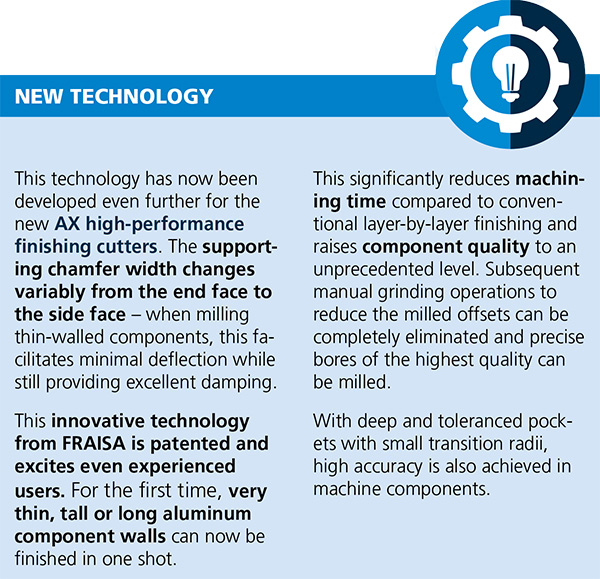
New machining strategy by combining roughing and finishing tools
Inspiring results can be achieved by using long roughing and finishing tools in combination with a new machining strategy. The key elements here are the programming strategy and the cutting data for the relevant component/machine situation.
The new AX finishing cutters open up new horizons as regards quality and performance. All information on the components depicted in this brochure can also be found in the application video and on our website.
Roughing and finishing combined
Roughing with AX-FPS
With AX-FPS technology, productivity and cost efficiency take absolute top priority. Positive, easy-cut geometries and mirror-finish flutes ensure excellent chip formation and good chip removal that benefits from a central coolant supply. This guarantees maximum performance.
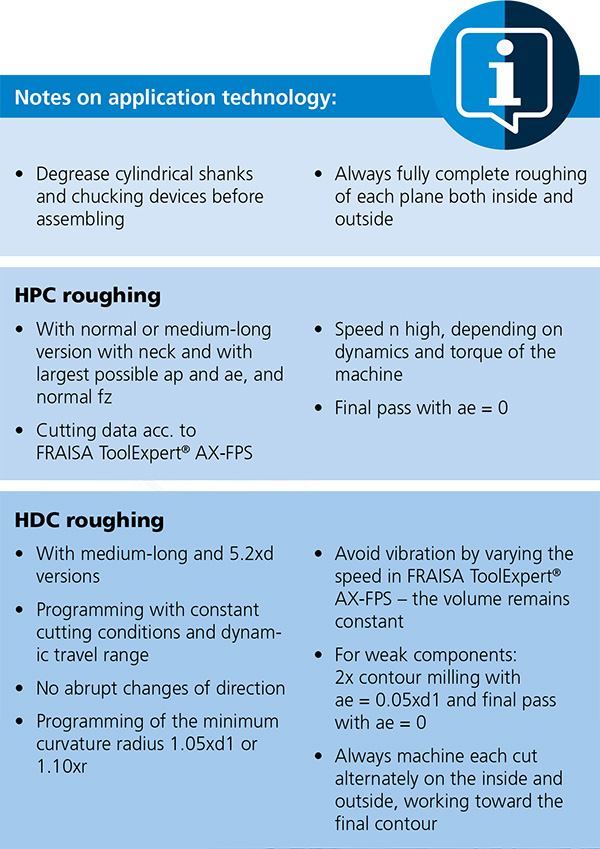
AX high-performance finishing cutters with revolutionary supporting chamfer technology
Unique and patented by FRAISA: The innovative supporting chamfer technology facilitates the finishing of thin-walled, tall and long component walls and sturdy components with deep finishing depths and greater radial engagement.
This unique tool concept is particularly impressive due to the fact that it offers extremely easy cutting with perfectly coordinated variable supporting chamfers and mirror-finish flutes and flanks for minimum adhesion.
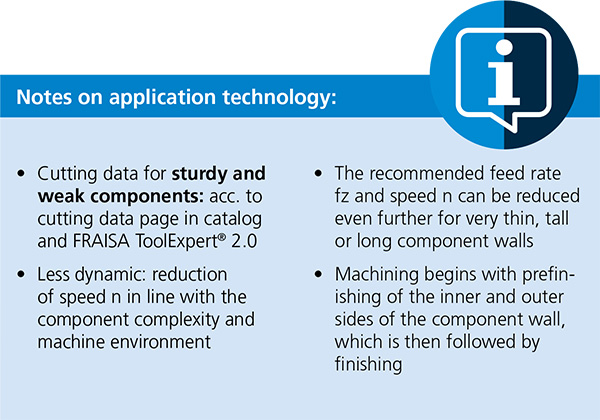
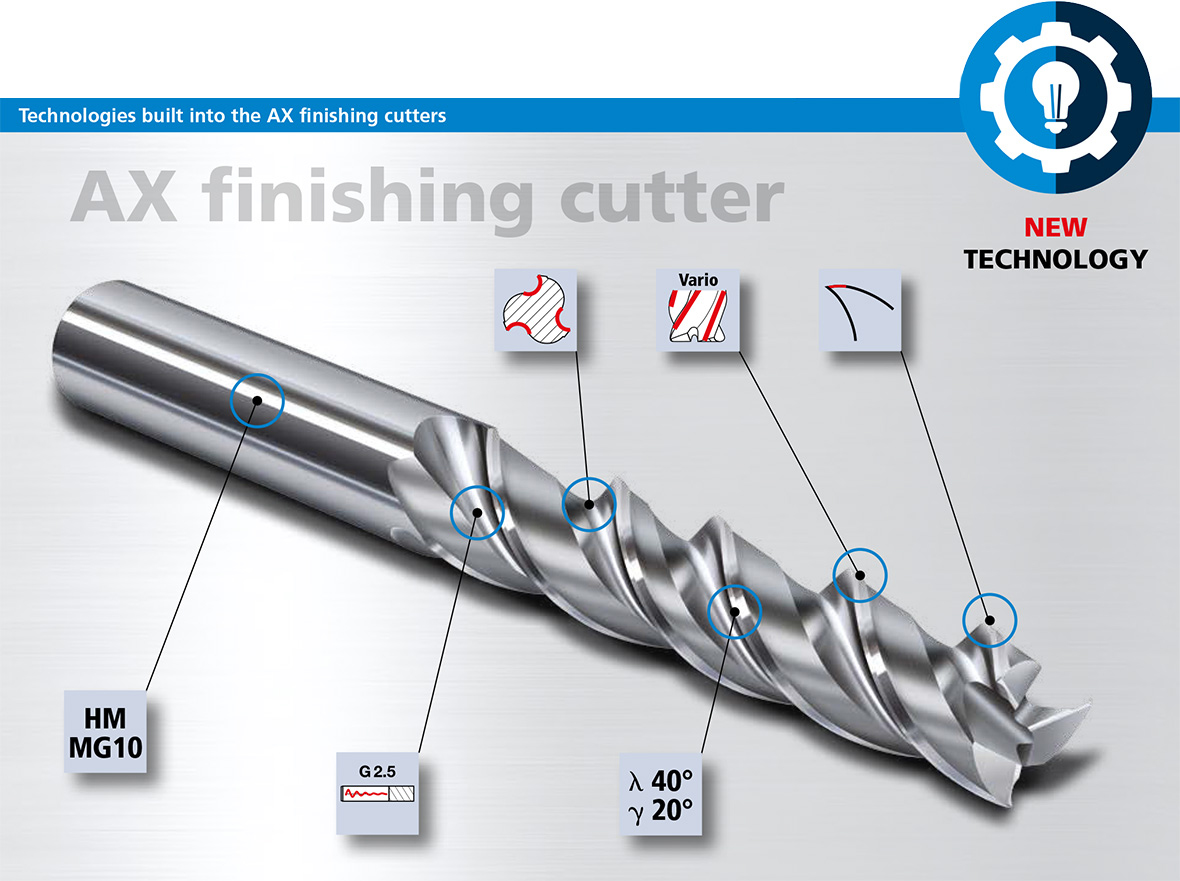
For detailed explanations of the tool technologies, please refer to the information section in the “High-performance Milling Tools” catalog.
Machining strategy for weak or thin-walled components
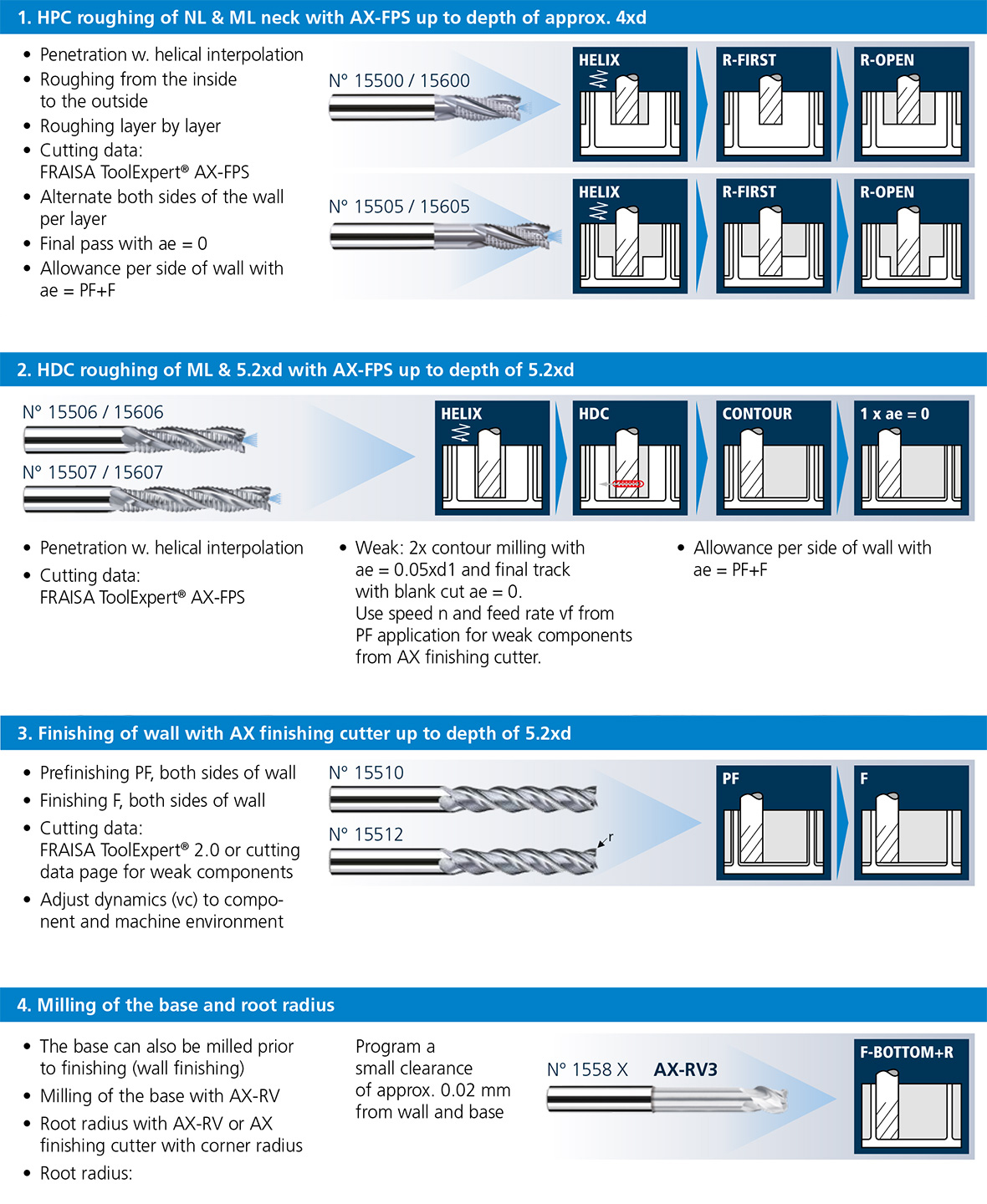
Optimization of the cutting data and machining strategy
The tool, cutting data, and machining strategy are selected on the basis of the component. The following notes on the individual component properties and their effect on the machining process can be used to optimize the manufacturing time and improve the manufacturing quality.
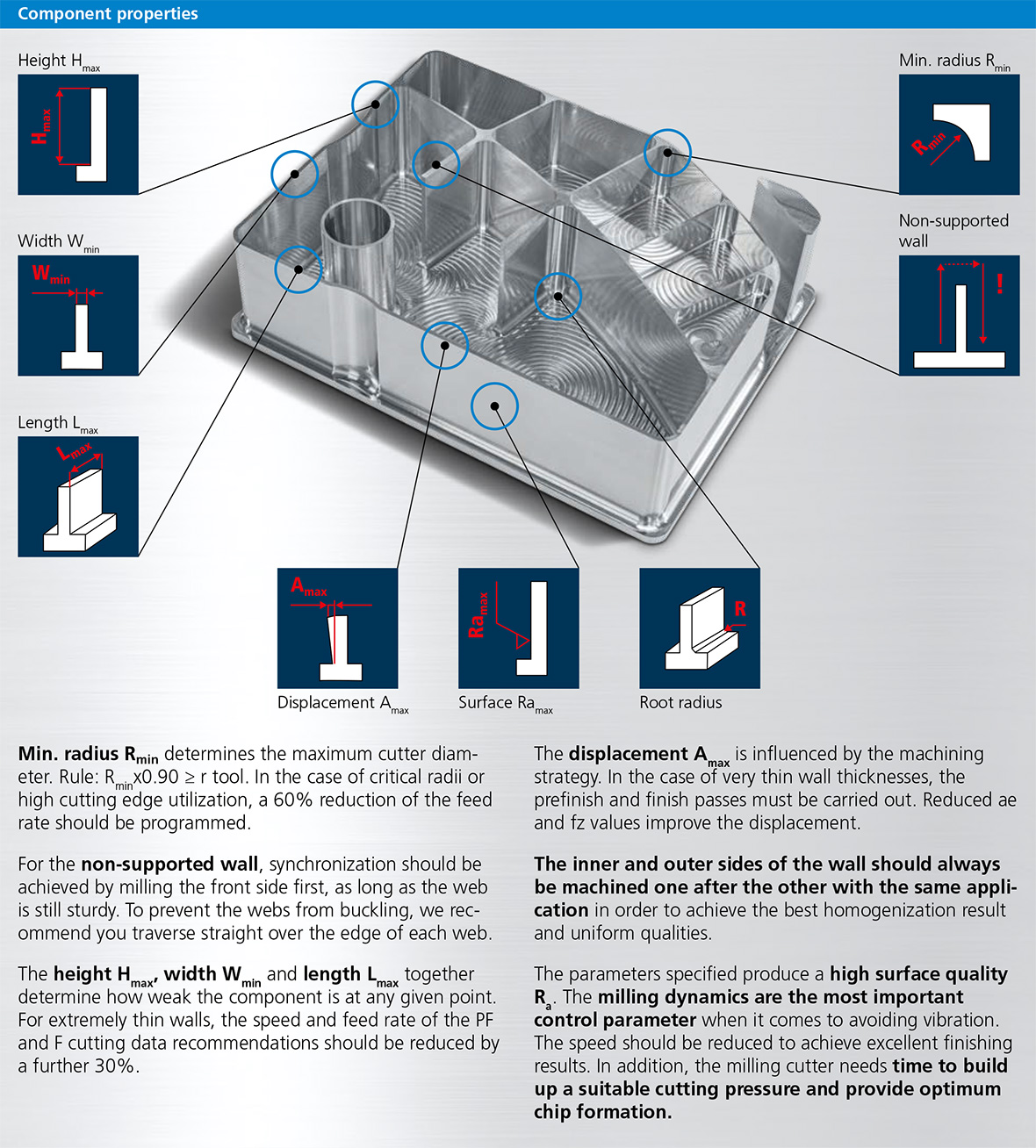
AX high-performance milling cutters for stabile components and newly added materials
AX-FPS and AX finishing cutters are ideal for a range of different materials such as copper, plastics and non-ferrous metals. The relevant cutting data can be found in FRAISA ToolExpert® 2.0 as well as in this brochure.
The advantage when machining sturdy component walls is the very low level of deflection of the AX finishing cutter combined with very smooth running. This enables precise fits with tight tolerances to be milled along the entire length of the cutting edge and a very high surface quality to be achieved.
High cutting edge utilization is also no problem for the AX finishing cutter – enabling bores with tight tolerances also to be produced without any difficulty. The machining strategy is similar to that for weak components. However, the “contour milling” step can be omitted when roughing depths of up to 5.2xd. The speed n and feed rate vf from the AX milling cutter for sturdy components and from the PF application should be used for the final track with blank cut ae = 0. The PF and F cutting data for sturdy components (classic finishing icon*) can also be used for finishing.
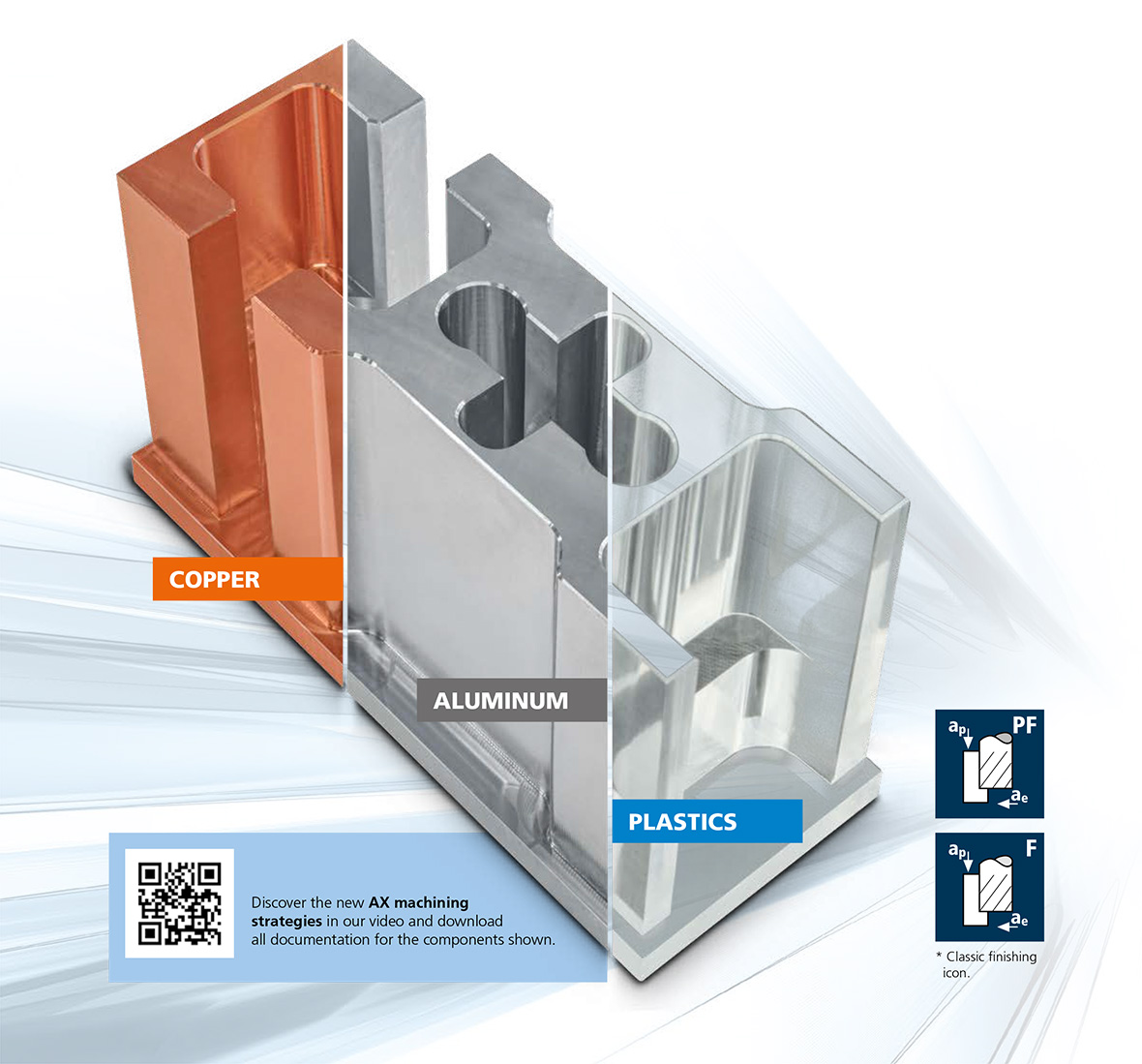