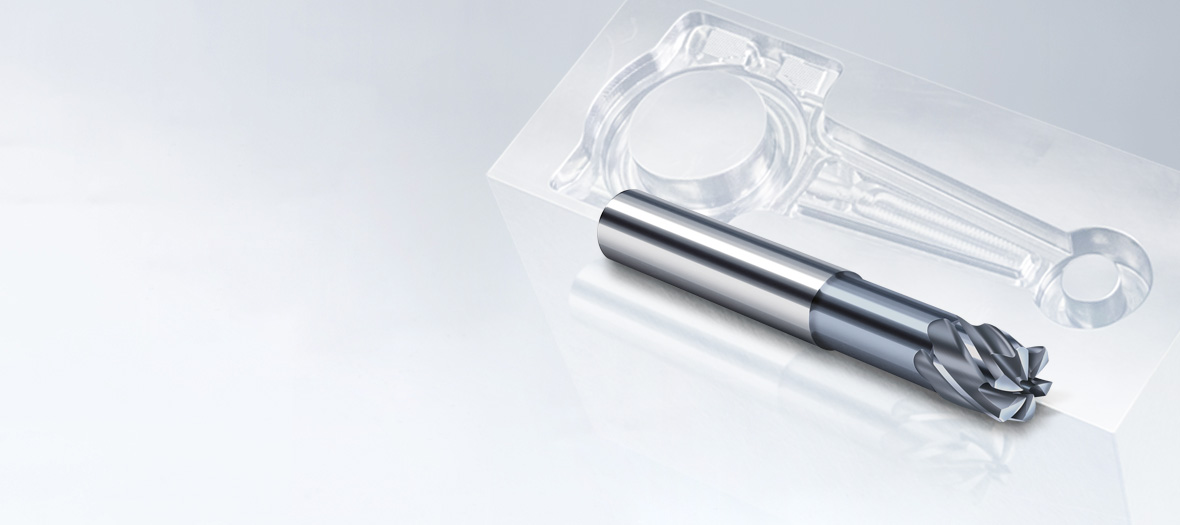
The new XFeed –
High Feed Productivity
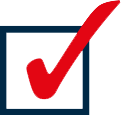
80 % higher infeeds
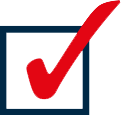
Productivity boost and very high chip removal rates (40%)
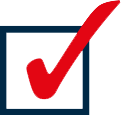
Safe and suitable for autonomous processes
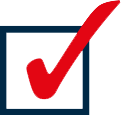
Sustainable thanks to
FRAISA ReTool®
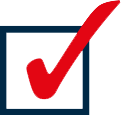
Extremely economical
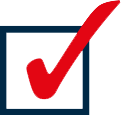
Verified application data
- Proven X-Al coating
- Optimized chip evacuation
- Robust 3D end cutting edge
- HM MG10 ultrafine-grain carbide
- Cutting edge conditioning
- New HFC edge geometry with cooling channel
XFeed – cycle start, walk away
With its new XFeed milling cutter, FRAISA has found the perfect solution for high-feed machining of medium- to high-strength steels. The new edge geometry facilitates maximum feed rates with higher axial infeeds for High Feed Cutting (HFC) processes. This means XFeed enables you to benefit from very high chip removal rates that cannot be achieved with conventional HFC tool concepts. Thanks to the very stable and low-vibration design, combined with precisely verified cutting data, machining processes can be carried out safely and autonomously with the new XFeed.
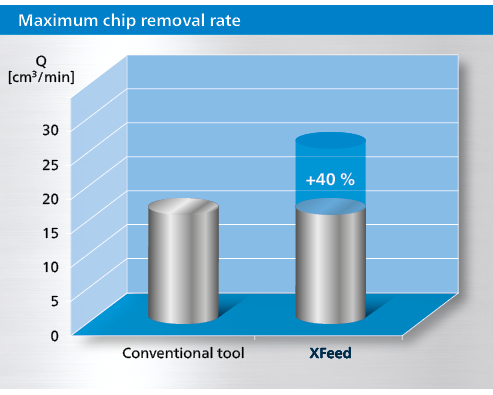
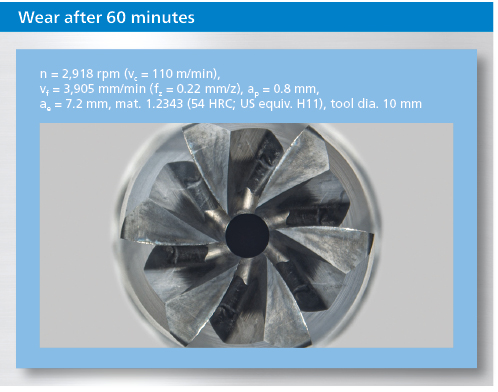
The family of XFeed tools is available in three different lengths of 3xd, 4.5xd and 6xd, allowing it to cover a wide range of applications. The carbide used is characterized by precisely matched degrees of robustness and hardness. In combination with the proven X-Al coating, this leads to excellent performance and a long tool life. The new shape of the cutting edge is predestined for use in highly dynamic machining processes. However, excellent chip removal rates can also be achieved on machines that are less dynamic. A central cooling channel ideally supports chip removal and is available in tools with a diameter of 6 mm or greater
Increasing productivity
With the new XFeed tool, the cutting edges form a radially and axially curved arc on a spherical segment. As a result, the chips are deliberately directed outwards during the chip formation process. This form of cutting edge guidance makes it possible to run high feed rates with deep cutting depths while still maintaining remarkable process stability. The central cooling channel ensures systematic cooling of the cutting edges, and the coolant also quickly and reliably conducts the chips out of the contact zone. This creates almost perfect conditions for obtaining good surfaces and a long tool life.
The face radius, in combination with the sickle-shaped cutting edge, enables low-vibration machining of hardened but also soft steels. The number of teeth, which is matched to the tool diameter, means a high level of performance can be achieved with all the tools in this family. The short cutting edges also mean the tools are rigid, which in turn improves their vibration behavior. XFeed tools can also be reconditioned multiple times by the FRAISA ReTool® service.
Final contour
The new cutting edge geometry of the XFeed tools adapts even better to the geometry of the lateral surface area. The subsequent finishing process can therefore be carried out even more efficiently than with conventional HFC tools.
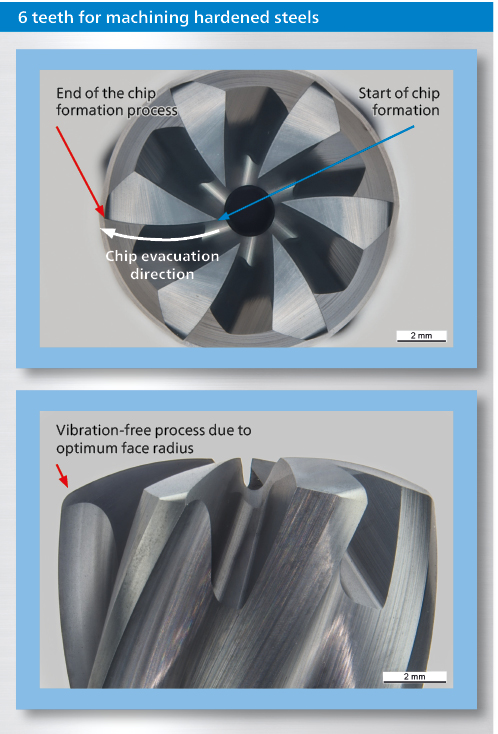